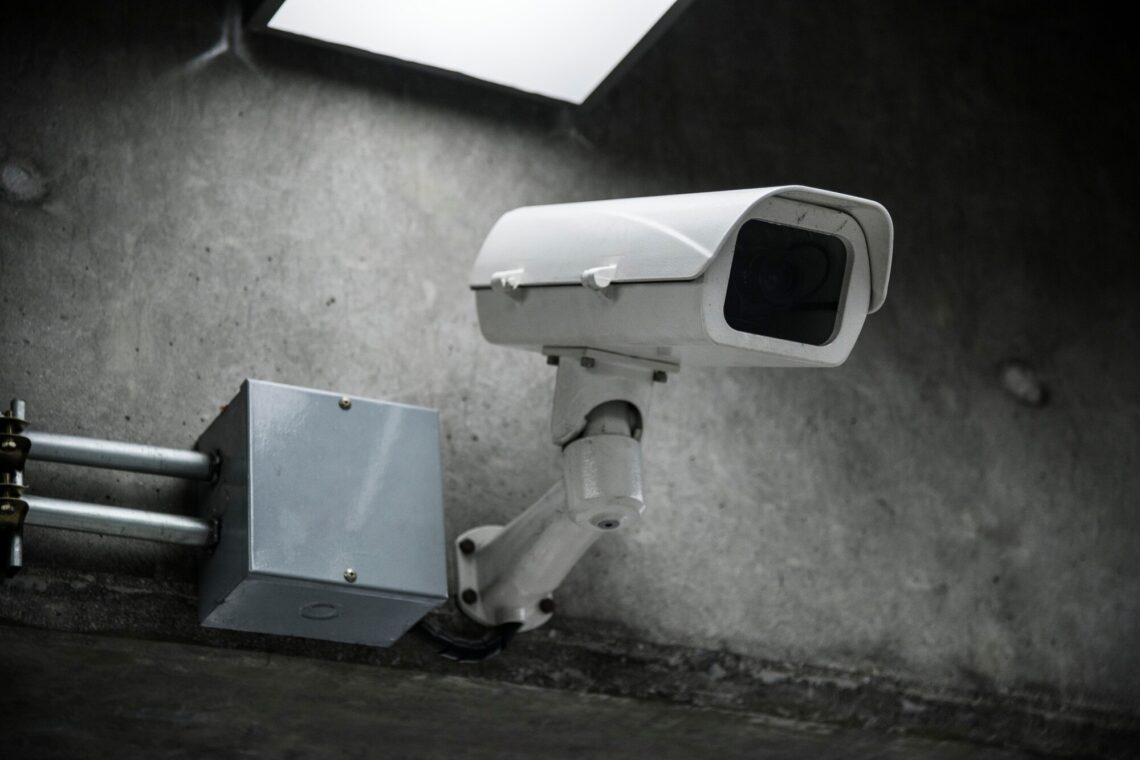
Ocena ryzyka w obiektach przemysłowych – metodologia identyfikacji i priorytetyzacji zagrożeń
Ocena ryzyka stanowi fundament efektywnego zarządzania bezpieczeństwem, pozwalając na identyfikację potencjalnych zagrożeń zanim przerodzą się w poważne incydenty. Niniejszy artykuł przedstawia szczegółową metodologię identyfikacji i priorytetyzacji zagrożeń w obiektach przemysłowych, dostarczając praktycznych wskazówek dla specjalistów BHP, inżynierów bezpieczeństwa oraz kadry zarządzającej.
Fundamenty oceny ryzyka w przemyśle – dlaczego to kluczowy element bezpieczeństwa?
Ocena ryzyka w obiektach przemysłowych to nie tylko wymóg prawny, ale przede wszystkim strategiczne narzędzie zarządzania bezpieczeństwem. Stanowi ona systematyczny proces identyfikacji potencjalnych zagrożeń, analizy prawdopodobieństwa ich wystąpienia oraz oceny możliwych konsekwencji. Właściwie przeprowadzona ocena ryzyka pozwala na podejmowanie świadomych decyzji dotyczących implementacji środków kontrolnych, które minimalizują ryzyko wystąpienia wypadków, awarii czy innych niepożądanych zdarzeń.
W kontekście obiektów przemysłowych, gdzie procesy produkcyjne często wiążą się z wykorzystaniem niebezpiecznych substancji, wysokich temperatur czy ciśnień, kompleksowa ocena ryzyka nabiera szczególnego znaczenia. Systematyczne podejście do identyfikacji zagrożeń stanowi podstawę do opracowania skutecznych strategii minimalizacji ryzyka, co przekłada się bezpośrednio na bezpieczeństwo pracowników, ochronę środowiska oraz ciągłość operacyjną przedsiębiorstwa.
Warto podkreślić, że ocena ryzyka nie jest jednorazowym działaniem, ale ciągłym procesem, który powinien być regularnie aktualizowany w odpowiedzi na zmiany w procesach produkcyjnych, wprowadzanie nowych technologii czy modyfikacje infrastruktury. Tylko takie podejście gwarantuje skuteczność w identyfikacji i zarządzaniu ryzykiem w dynamicznie zmieniającym się środowisku przemysłowym.
Prawne aspekty oceny ryzyka – co mówią przepisy?
Kwestie związane z oceną ryzyka w obiektach przemysłowych są regulowane przez szereg aktów prawnych, zarówno na poziomie krajowym, jak i międzynarodowym. W Unii Europejskiej kluczowym dokumentem jest Dyrektywa Maszynowa 2006/42/WE, która nakłada na producentów maszyn obowiązek przeprowadzenia analizy ryzyka przed wprowadzeniem produktu na rynek. Od 2027 roku zacznie obowiązywać nowe Rozporządzenie Parlamentu Europejskiego i Rady (UE) 2023/1230 z dnia 14 czerwca 2023 r., które wprowadza dodatkowe wymagania w zakresie oceny ryzyka.
Kluczowe regulacje prawne dotyczące oceny ryzyka obejmują:
- Obowiązek przeprowadzenia oceny ryzyka dla każdej maszyny przed wprowadzeniem jej na rynek
- Konieczność dokumentowania procesu oceny ryzyka
- Wymóg regularnej aktualizacji oceny ryzyka w odpowiedzi na zmiany w procesach produkcyjnych
- Obowiązek konsultowania wyników oceny ryzyka z pracownikami lub ich przedstawicielami
Warto zaznaczyć, że choć przepisy nakładają obowiązek przeprowadzenia oceny ryzyka, nie precyzują konkretnej metodologii, pozostawiając wybór odpowiedniej metody w gestii pracodawcy. Takie podejście pozwala na dostosowanie metodyki oceny ryzyka do specyfiki danego przedsiębiorstwa, uwzględniając charakter prowadzonej działalności, stosowane technologie oraz poziom kompetencji personelu.
Etapy procesu oceny ryzyka – kompleksowe podejście krok po kroku
Proces oceny ryzyka w obiektach przemysłowych składa się z kilku kluczowych etapów, które tworzą spójną metodologię identyfikacji i priorytetyzacji zagrożeń. Poniżej przedstawiono szczegółowy opis poszczególnych kroków, które należy podjąć w celu przeprowadzenia kompleksowej oceny ryzyka.
Etap 1: Zbieranie niezbędnych informacji
Pierwszym krokiem w procesie oceny ryzyka jest zgromadzenie wszystkich istotnych informacji dotyczących analizowanego obiektu przemysłowego. Kluczowe źródła informacji obejmują:
- Dokumentację techniczno-eksploatacyjną maszyn i urządzeń
- Rejestry wypadków i chorób zawodowych
- Wyniki pomiarów czynników szkodliwych i niebezpiecznych
- Karty charakterystyki substancji chemicznych wykorzystywanych w procesach produkcyjnych
- Instrukcje stanowiskowe i procedury operacyjne
- Raporty z wcześniejszych ocen ryzyka i audytów bezpieczeństwa
Kompleksowe podejście do zbierania informacji pozwala na uzyskanie pełnego obrazu potencjalnych zagrożeń występujących w analizowanym obiekcie. Warto również uwzględnić wiedzę i doświadczenie pracowników, którzy często posiadają cenne spostrzeżenia dotyczące zagrożeń związanych z wykonywanymi przez nich zadaniami.
Etap 2: Identyfikacja zagrożeń
Identyfikacja zagrożeń stanowi fundament procesu oceny ryzyka. Na tym etapie należy wskazać wszystkie warunki środowiska pracy, które mogą powodować niebezpieczeństwo dla zdrowia pracowników wykonujących konkretne zadania. Systematyczne podejście do identyfikacji zagrożeń powinno uwzględniać:
- Zagrożenia mechaniczne (np. ruchome części maszyn, ostre krawędzie)
- Zagrożenia elektryczne (np. ryzyko porażenia prądem)
- Zagrożenia termiczne (np. gorące powierzchnie, materiały)
- Zagrożenia chemiczne (np. toksyczne substancje, łatwopalne materiały)
- Zagrożenia biologiczne (np. patogeny, alergeny)
- Zagrożenia ergonomiczne (np. niewłaściwa pozycja ciała, powtarzalne ruchy)
- Zagrożenia związane z czynnikami fizycznymi (np. hałas, wibracje, promieniowanie)
Warto podkreślić, że identyfikacja zagrożeń powinna obejmować nie tylko standardowe operacje, ale również zadania wykonywane sporadycznie, takie jak konserwacja, czyszczenie czy naprawy. Kompleksowa identyfikacja zagrożeń wymaga analizy wszystkich etapów cyklu życia maszyn i urządzeń, od instalacji, przez eksploatację, aż po demontaż i złomowanie.
Etap 3: Oszacowanie ryzyka
Po zidentyfikowaniu wszystkich potencjalnych zagrożeń, kolejnym krokiem jest oszacowanie związanego z nimi ryzyka. Na tym etapie określa się prawdopodobieństwo wystąpienia niepożądanych następstw danego zagrożenia oraz ciężkość tych następstw. W zależności od wybranej metody oceny ryzyka, proces szacowania może uwzględniać różne parametry.
Celem oszacowania ryzyka jest kwantyfikacja ryzyka przy użyciu określonych wcześniej parametrów oraz przedstawienie ryzyka przy pomocy wskaźnika liczbowego lub opisowego. Wynik tego etapu stanowi podstawę do określenia, czy dane ryzyko jest akceptowalne, czy też wymaga podjęcia działań korygujących.
Etap 4: Wartościowanie ryzyka
Wartościowanie ryzyka polega na określeniu, czy zidentyfikowane zagrożenia zostały wyeliminowane, a jeśli nie, to czy istnieje realna możliwość redukcji ryzyka. Na tym etapie porównuje się oszacowane ryzyko z przyjętymi kryteriami akceptowalności, co pozwala na podjęcie decyzji odnośnie do konieczności implementacji dodatkowych środków kontrolnych.
W zależności od uzyskanych wyników oszacowania ryzyka można:
- Wykonać niezbędną dokumentację, jeśli ryzyko zostało zredukowane w odpowiednim stopniu
- Wprowadzić zmiany konstrukcyjne, jeśli są one możliwe i mogą przyczynić się do zmniejszenia ryzyka
- Zmniejszyć ryzyko za pomocą technicznych środków ochronnych, jeśli nie można wprowadzić zmian projektowych
- Zmniejszyć ryzyko poprzez poinformowanie użytkownika co do sposobu użytkowania maszyny oraz istnieniu zagrożeń resztkowych
Etap 5: Opracowanie działań korygujących
Na podstawie wyników wartościowania ryzyka, należy opracować plan działań korygujących, mających na celu eliminację lub ograniczenie zidentyfikowanych zagrożeń. Hierarchia środków kontroli ryzyka obejmuje:
- Eliminację zagrożenia (np. zastąpienie niebezpiecznego procesu bezpieczniejszą alternatywą)
- Zastąpienie (np. wymiana niebezpiecznych substancji na mniej szkodliwe)
- Środki techniczne (np. instalacja osłon, barier, systemów wentylacyjnych)
- Środki administracyjne (np. procedury, szkolenia, rotacja pracowników)
- Środki ochrony indywidualnej (np. kaski, okulary ochronne, rękawice)
Przy opracowywaniu działań korygujących należy kierować się zasadą ALARP (As Low As Reasonably Practicable), dążąc do redukcji ryzyka do poziomu tak niskiego, jak to praktycznie możliwe, uwzględniając jednocześnie aspekty techniczne, ekonomiczne i operacyjne.
Etap 6: Wdrożenie i monitorowanie
Ostatnim, ale nie mniej istotnym etapem procesu oceny ryzyka jest wdrożenie opracowanych działań korygujących oraz monitorowanie ich skuteczności. Kluczowe elementy tego etapu obejmują:
- Opracowanie harmonogramu wdrożenia działań korygujących
- Przydzielenie odpowiedzialności za realizację poszczególnych zadań
- Zapewnienie niezbędnych zasobów (finansowych, technicznych, ludzkich)
- Monitorowanie postępów we wdrażaniu działań korygujących
- Ocena skuteczności zaimplementowanych środków kontrolnych
- Aktualizacja oceny ryzyka w odpowiedzi na zmiany w procesach produkcyjnych lub środowisku pracy
Warto podkreślić, że ocena ryzyka nie jest jednorazowym działaniem, ale ciągłym procesem, który wymaga regularnej weryfikacji i aktualizacji. Tylko takie podejście gwarantuje skuteczność w identyfikacji i zarządzaniu ryzykiem w dynamicznie zmieniającym się środowisku przemysłowym.
Metody oceny ryzyka – wybór optymalnego podejścia
Istnieje wiele metod oceny ryzyka, które można zastosować w obiektach przemysłowych. Wybór odpowiedniej metody zależy od specyfiki analizowanego obiektu, dostępnych zasobów oraz poziomu kompetencji osób przeprowadzających ocenę. Poniżej przedstawiono najpopularniejsze metody oceny ryzyka stosowane w przemyśle.
Metoda Risk Score – ilościowa ocena wskaźnika ryzyka
Metoda Risk Score należy do jakościowych metod oceny ryzyka w miejscu pracy i składa się z czterech etapów. Jest to jedna z najpopularniejszych metod stosowanych w przemyśle, która pozwala na ilościową ocenę ryzyka poprzez przypisanie wartości liczbowych poszczególnym parametrom.
Kluczowe elementy metody Risk Score:
- Określenie i opisanie obszaru występowania zagrożenia
- Sporządzenie listy zidentyfikowanych zagrożeń
- Oszacowanie ryzyka dla danego zagrożenia według wzoru: R = P × E × S, gdzie:
- R – wskaźnik ryzyka
- P – wskaźnik prawdopodobieństwa wystąpienia zdarzenia wypadkowego
- E – czas ekspozycji na czynnik niebezpieczny
- S – możliwe skutki oraz ich ciężkość
- Wartościowanie ryzyka na podstawie uzyskanego wskaźnika
Zaletą metody Risk Score jest jej uniwersalność oraz możliwość ilościowego porównania różnych rodzajów ryzyka. Dzięki temu można łatwo określić priorytety w zakresie implementacji działań korygujących, koncentrując się na zagrożeniach o najwyższym wskaźniku ryzyka.
Metoda JSA (Job Safety Analysis) – analiza bezpieczeństwa pracy
Metoda JSA (Job Safety Analysis) jest metodą indukcyjną, która zakłada, że ryzyko zawodowe jest funkcją prawdopodobieństwa zdarzenia i jego konsekwencji. Metoda ta koncentruje się na analizie poszczególnych zadań wykonywanych przez pracowników, identyfikując potencjalne zagrożenia związane z każdym etapem pracy.
Proces oceny ryzyka metodą JSA obejmuje:
- Określenie granic obiektu
- Sporządzenie listy zagrożeń
- Oszacowanie ryzyka według wzoru: P = F × O × A, gdzie:
- P – prawdopodobieństwo konsekwencji
- F – częstotliwość wystąpienia zagrożeń
- O – prawdopodobieństwo zagrożeń
- A – możliwość uniknięcia lub ograniczenia szkody
- Wartościowanie ryzyka
Metoda JSA jest szczególnie przydatna w analizie złożonych procesów produkcyjnych, gdzie pracownicy wykonują różnorodne zadania. Pozwala na szczegółową analizę każdego etapu pracy, identyfikując potencjalne zagrożenia i opracowując odpowiednie środki kontrolne.
Metoda PHA (Preliminary Hazard Analysis) – wstępna analiza zagrożeń
Metoda PHA (Preliminary Hazard Analysis) to jakościowa metoda oceny ryzyka, której głównym celem jest określenie możliwości powstania wypadku oraz możliwych skutków wypadku i ewentualną utratę zdrowia. Jest to metoda szczególnie przydatna na wczesnych etapach projektowania systemów lub procesów, gdy dostępne są ograniczone informacje.
Etapy oceny ryzyka metodą PHA:
- Określenie granic obiektów, dla którego przeprowadza się ocenę
- Stworzenie listy wszystkich zidentyfikowanych zagrożeń występujących na ocenianym stanowisku pracy
- Oszacowanie ryzyka według wzoru: W = S × P, gdzie:
- W – wskaźnik ryzyka
- S – stopień szkód
- P – prawdopodobieństwo szkód zdarzenia
- Wartościowanie ryzyka
Metoda PHA jest szczególnie przydatna na etapie projektowania nowych instalacji lub procesów, pozwalając na wczesną identyfikację potencjalnych zagrożeń i implementację odpowiednich środków kontrolnych już na etapie koncepcyjnym.
Metoda HAZOP (Hazard and Operability Study) – analiza zagrożeń i zdolności operacyjnych
Metoda HAZOP (Hazard and Operability Study) to systematyczne i kompleksowe narzędzie, które pozwala na identyfikację potencjalnych zagrożeń już na etapie projektowania instalacji przemysłowych. Jest to metoda szczególnie popularna w przemyśle chemicznym, petrochemicznym i farmaceutycznym, gdzie procesy produkcyjne często wiążą się z wykorzystaniem niebezpiecznych substancji.
Kluczowe elementy metody HAZOP:
- Wykorzystanie charakterystycznych słów kluczowych, takich jak “więcej”, “mniej”, “odwrotnie” czy “brak”, do identyfikacji możliwych odchyleń od normalnych warunków procesowych
- Analiza potencjalnych przyczyn i konsekwencji zidentyfikowanych odchyleń
- Opracowanie rekomendacji mających na celu eliminację lub ograniczenie zidentyfikowanych zagrożeń
Metoda HAZOP jest szczególnie skuteczna w identyfikacji zagrożeń związanych z odchyleniami od normalnych warunków procesowych, co czyni ją niezwykle wartościowym narzędziem w analizie złożonych procesów przemysłowych.
Metoda C-HAZOP (Control Hazard and Operability Studies) – analiza zagrożeń i zdolności operacyjnych systemów sterowania
Metoda C-HAZOP (Control Hazard and Operability Studies) to rozszerzenie klasycznej metody HAZOP, koncentrujące się na analizie systemów sterowania. Metoda ta pomaga zminimalizować ryzyko awarii, zwiększyć bezpieczeństwo oraz zoptymalizować procesy produkcyjne poprzez identyfikację potencjalnych zagrożeń związanych z systemami sterowania.
Zastosowanie metody C-HAZOP obejmuje:
- Identyfikację potencjalnych błędów w systemach sterowania
- Analizę konsekwencji zidentyfikowanych błędów
- Opracowanie rekomendacji mających na celu zwiększenie niezawodności systemów sterowania
W dobie rosnącej automatyzacji procesów przemysłowych, metoda C-HAZOP zyskuje na znaczeniu, pozwalając na kompleksową analizę zagrożeń związanych z systemami sterowania, które stanowią kluczowy element nowoczesnych instalacji przemysłowych.
Identyfikacja zagrożeń w obiektach przemysłowych – kompleksowe podejście
Identyfikacja zagrożeń stanowi fundament procesu oceny ryzyka. W obiektach przemysłowych, gdzie procesy produkcyjne często wiążą się z wykorzystaniem niebezpiecznych substancji, wysokich temperatur czy ciśnień, kompleksowa identyfikacja zagrożeń nabiera szczególnego znaczenia. Poniżej przedstawiono szczegółowe podejście do identyfikacji zagrożeń w obiektach przemysłowych.
Klasyfikacja zagrożeń w środowisku przemysłowym
W zależności od charakteru działania, niebezpieczne i szkodliwe czynniki występujące w procesie pracy dzieli się na cztery główne grupy:
- Zagrożenia fizyczne:
- Hałas i wibracje
- Promieniowanie (jonizujące, niejonizujące)
- Ekstremalne temperatury
- Ciśnienie (nadciśnienie, podciśnienie)
- Elektryczność
- Ruchome części maszyn
- Ostre krawędzie
- Śliskie powierzchnie
- Zagrożenia chemiczne:
- Substancje toksyczne
- Substancje żrące
- Substancje łatwopalne
- Substancje wybuchowe
- Substancje rakotwórcze
- Substancje mutagenne
- Substancje działające szkodliwie na rozrodczość
- Zagrożenia biologiczne:
- Bakterie
- Wirusy
- Grzyby
- Pasożyty
- Alergeny
- Zagrożenia ergonomiczne:
- Niewłaściwa pozycja ciała
- Powtarzalne ruchy
- Nadmierny wysiłek fizyczny
- Monotonia pracy
- Stres
Kompleksowa identyfikacja zagrożeń wymaga uwzględnienia wszystkich powyższych kategorii, analizując każdy etap procesu produkcyjnego pod kątem potencjalnych zagrożeń dla zdrowia i bezpieczeństwa pracowników.
Metody identyfikacji zagrożeń
Istnieje wiele metod identyfikacji zagrożeń, które można zastosować w obiektach przemysłowych. Wybór odpowiedniej metody zależy od specyfiki analizowanego obiektu, dostępnych zasobów oraz poziomu kompetencji osób przeprowadzających ocenę. Poniżej przedstawiono najpopularniejsze metody identyfikacji zagrożeń stosowane w przemyśle:
- Obserwacja środowiska pracy – bezpośrednia obserwacja procesów produkcyjnych, maszyn i urządzeń oraz zachowań pracowników
- Obserwacja zadań wykonywanych na stanowisku pracy – analiza poszczególnych etapów pracy pod kątem potencjalnych zagrożeń
- Wywiady z pracownikami – zbieranie informacji od osób bezpośrednio zaangażowanych w procesy produkcyjne
- Analiza dokumentacji – przegląd dokumentacji technicznej, instrukcji stanowiskowych, wyników badań i pomiarów czynników szkodliwych, kart charakterystyki substancji chemicznych, dokumentacji dotyczącej wypadków przy pracy i chorób zawodowych
- Analiza literatury technicznej – identyfikacja zagrożeń charakterystycznych dla danej branży lub rodzaju prac
- Listy kontrolne – wykorzystanie standardowych list kontrolnych, zawierających pytania umożliwiające stwierdzenie spełniania przez użytkowane maszyny wymagań minimalnych
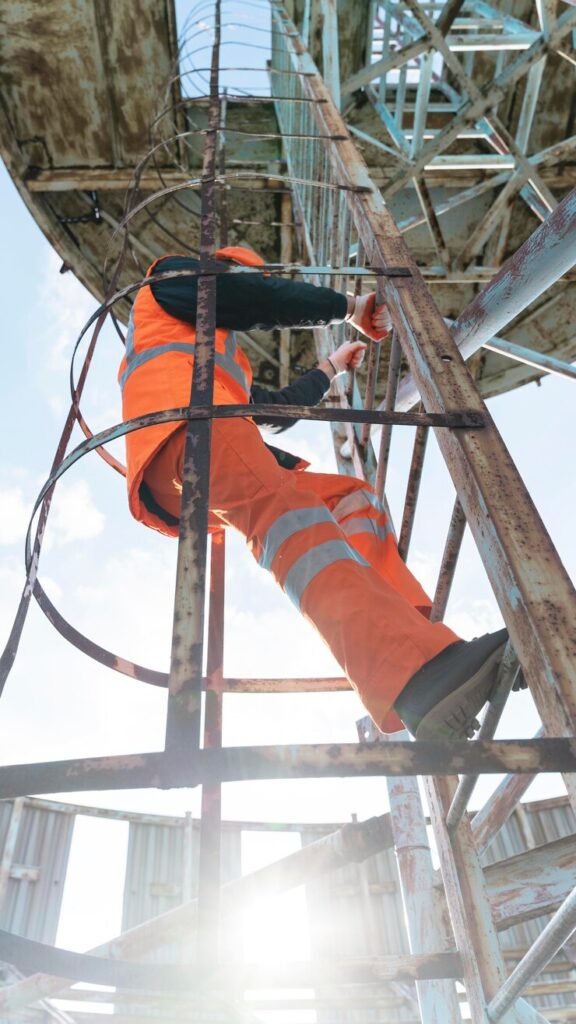
Priorytetyzacja zagrożeń – skuteczne zarządzanie ryzykiem
Priorytetyzacja zagrożeń to kluczowy element procesu oceny ryzyka, który pozwala na efektywne zarządzanie ograniczonymi zasobami poprzez koncentrację na zagrożeniach o najwyższym poziomie ryzyka. W obiektach przemysłowych, gdzie często występuje wiele różnorodnych zagrożeń, właściwa priorytetyzacja nabiera szczególnego znaczenia.
Matryca ryzyka – narzędzie do priorytetyzacji zagrożeń
Jednym z najpopularniejszych narzędzi do priorytetyzacji zagrożeń jest matryca ryzyka, która pozwala na wizualne przedstawienie poziomu ryzyka związanego z poszczególnymi zagrożeniami. Matryca ryzyka uwzględnia dwa kluczowe parametry:
- Prawdopodobieństwo wystąpienia zdarzenia – określa, jak prawdopodobne jest, że dane zagrożenie spowoduje niepożądane zdarzenie
- Konsekwencje zdarzenia – określa potencjalne skutki zdarzenia dla zdrowia i życia pracowników, środowiska naturalnego oraz mienia
Typowa matryca ryzyka ma formę tabeli, w której wiersze reprezentują różne poziomy prawdopodobieństwa, a kolumny – różne poziomy konsekwencji. Na przecięciu wiersza i kolumny znajduje się poziom ryzyka, który może być wyrażony liczbowo lub opisowo (np. niskie, średnie, wysokie, ekstremalne).
Zagrożenia o najwyższym poziomie ryzyka powinny być traktowane priorytetowo i wymagają natychmiastowych działań korygujących. Zagrożenia o średnim poziomie ryzyka wymagają zaplanowania działań korygujących w określonym czasie, natomiast zagrożenia o niskim poziomie ryzyka mogą być akceptowalne, ale powinny być monitorowane.
Kryteria priorytetyzacji zagrożeń
Przy priorytetyzacji zagrożeń należy uwzględnić szereg kryteriów, które pozwalają na kompleksową ocenę znaczenia poszczególnych zagrożeń. Kluczowe kryteria priorytetyzacji obejmują:
- Potencjalne skutki dla zdrowia i życia pracowników – zagrożenia mogące spowodować poważne obrażenia lub śmierć powinny być traktowane priorytetowo
- Liczba narażonych osób – zagrożenia, na które narażona jest większa liczba pracowników, powinny mieć wyższy priorytet
- Częstotliwość ekspozycji – zagrożenia, na które pracownicy są narażeni częściej lub przez dłuższy czas, powinny mieć wyższy priorytet
- Możliwość eliminacji lub ograniczenia zagrożenia – zagrożenia, które można łatwo wyeliminować lub ograniczyć, mogą być traktowane priorytetowo ze względu na szybkie efekty
- Koszty implementacji środków kontrolnych – przy ograniczonych zasobach, należy uwzględnić efektywność kosztową działań korygujących
- Wymagania prawne – zagrożenia związane z naruszeniem przepisów prawnych powinny być traktowane priorytetowo
Właściwa priorytetyzacja zagrożeń pozwala na optymalne wykorzystanie dostępnych zasobów oraz koncentrację na działaniach, które przyniosą największe korzyści w zakresie poprawy bezpieczeństwa w obiekcie przemysłowym.
Zarządzanie ryzykiem resztkowym – nieunikniony element bezpieczeństwa
Pomimo wdrożenia odpowiednich środków kontrolnych, całkowita eliminacja ryzyka w obiektach przemysłowych jest często niemożliwa. Ryzyko, które pozostaje po zastosowaniu wszystkich możliwych środków kontrolnych, nazywane jest ryzykiem resztkowym. Właściwe zarządzanie ryzykiem resztkowym stanowi kluczowy element kompleksowego podejścia do bezpieczeństwa w przemyśle.
Identyfikacja i ocena ryzyka resztkowego
Pierwszym krokiem w zarządzaniu ryzykiem resztkowym jest jego identyfikacja i ocena. Po wdrożeniu środków kontrolnych należy ponownie przeprowadzić ocenę ryzyka, aby określić, jakie zagrożenia pozostały i jaki jest poziom związanego z nimi ryzyka. Kluczowe elementy oceny ryzyka resztkowego obejmują:
- Identyfikację zagrożeń, które nie zostały całkowicie wyeliminowane
- Ocenę skuteczności wdrożonych środków kontrolnych
- Określenie poziomu ryzyka resztkowego dla każdego zidentyfikowanego zagrożenia
- Ocenę akceptowalności ryzyka resztkowego
Ryzyko resztkowe powinno być tak niskie, jak to praktycznie możliwe (ALARP – As Low As Reasonably Practicable), uwzględniając aspekty techniczne, ekonomiczne i operacyjne.
Strategie zarządzania ryzykiem resztkowym
Istnieje kilka strategii zarządzania ryzykiem resztkowym, które można zastosować w obiektach przemysłowych. Wybór odpowiedniej strategii zależy od poziomu ryzyka resztkowego, dostępnych zasobów oraz specyfiki analizowanego obiektu. Popularne strategie zarządzania ryzykiem resztkowym obejmują:
- Akceptacja ryzyka – w przypadku niskiego poziomu ryzyka resztkowego, można podjąć świadomą decyzję o jego akceptacji, pod warunkiem regularnego monitorowania
- Transfer ryzyka – przeniesienie odpowiedzialności za ryzyko na inny podmiot, np. poprzez ubezpieczenie
- Dodatkowe środki kontrolne – implementacja dodatkowych środków technicznych lub organizacyjnych w celu dalszej redukcji ryzyka
- Ograniczenie ekspozycji – zmniejszenie czasu ekspozycji pracowników na dane zagrożenie
- Szkolenia i informowanie – podnoszenie świadomości pracowników na temat istniejących zagrożeń i sposobów bezpiecznego wykonywania pracy
Niezależnie od wybranej strategii, kluczowe znaczenie ma komunikacja ryzyka resztkowego wszystkim osobom, które mogą być na nie narażone. Pracownicy powinni być świadomi istniejących zagrożeń oraz znać procedury bezpiecznego wykonywania pracy w ich obecności.
Wdrażanie programów redukcji ryzyka – od teorii do praktyki
Opracowanie planu działań korygujących to dopiero początek procesu redukcji ryzyka. Kluczowym elementem jest skuteczne wdrożenie zaplanowanych działań, co wymaga systematycznego podejścia oraz zaangażowania wszystkich poziomów organizacji. Poniżej przedstawiono praktyczne wskazówki dotyczące wdrażania programów redukcji ryzyka w obiektach przemysłowych.
Planowanie wdrożenia
Pierwszym krokiem w procesie wdrażania programu redukcji ryzyka jest opracowanie szczegółowego planu wdrożenia. Kluczowe elementy planu wdrożenia obejmują:
- Określenie celów i oczekiwanych rezultatów
- Identyfikację niezbędnych zasobów (finansowych, technicznych, ludzkich)
- Opracowanie harmonogramu wdrożenia
- Przydzielenie odpowiedzialności za realizację poszczególnych zadań
- Określenie wskaźników efektywności, które pozwolą na monitorowanie postępów
Plan wdrożenia powinien być realistyczny i uwzględniać specyfikę organizacji, w tym dostępne zasoby, kulturę organizacyjną oraz poziom kompetencji personelu.
Zaangażowanie pracowników
Skuteczne wdrożenie programu redukcji ryzyka wymaga zaangażowania wszystkich pracowników, od najwyższego kierownictwa po pracowników operacyjnych. Kluczowe elementy budowania zaangażowania obejmują:
- Komunikację celów i korzyści programu redukcji ryzyka
- Włączenie pracowników w proces identyfikacji zagrożeń i opracowania działań korygujących
- Zapewnienie odpowiednich szkoleń i wsparcia
- Uznanie i nagradzanie zaangażowania w poprawę bezpieczeństwa
- Regularne informowanie o postępach i osiągniętych rezultatach
Zaangażowanie pracowników jest szczególnie istotne, ponieważ to oni często najlepiej znają specyfikę swojej pracy i mogą zidentyfikować potencjalne problemy związane z wdrażaniem nowych rozwiązań.
Monitorowanie i ocena skuteczności
Wdrożenie programu redukcji ryzyka nie kończy procesu zarządzania ryzykiem. Konieczne jest regularne monitorowanie i ocena skuteczności wdrożonych działań, co pozwala na identyfikację obszarów wymagających dalszej poprawy. Kluczowe elementy monitorowania i oceny skuteczności obejmują:
- Regularne audyty i inspekcje
- Analiza wskaźników bezpieczeństwa (np. liczba wypadków, zdarzeń potencjalnie wypadkowych)
- Zbieranie informacji zwrotnych od pracowników
- Przegląd i aktualizacja oceny ryzyka
- Identyfikacja nowych zagrożeń lub zmian w istniejących zagrożeniach
Wyniki monitorowania i oceny skuteczności powinny być wykorzystywane do ciągłego doskonalenia programu redukcji ryzyka, co jest zgodne z podejściem cyklu PDCA (Plan-Do-Check-Act).
Rola technologii w ocenie ryzyka – nowoczesne narzędzia i rozwiązania
W dobie cyfrowej transformacji, technologia odgrywa coraz większą rolę w procesie oceny ryzyka w obiektach przemysłowych. Nowoczesne narzędzia i rozwiązania pozwalają na bardziej efektywną identyfikację zagrożeń, analizę ryzyka oraz monitorowanie skuteczności wdrożonych środków kontrolnych. Poniżej przedstawiono wybrane technologie, które znajdują zastosowanie w ocenie ryzyka.
Systemy zarządzania bezpieczeństwem (SMS)
Systemy zarządzania bezpieczeństwem (Safety Management Systems) to kompleksowe rozwiązania informatyczne, które wspierają proces zarządzania bezpieczeństwem w organizacji. Kluczowe funkcjonalności systemów SMS obejmują:
- Rejestrację i analizę zdarzeń wypadkowych i potencjalnie wypadkowych
- Zarządzanie ocenami ryzyka
- Monitorowanie wdrażania działań korygujących
- Zarządzanie szkoleniami z zakresu bezpieczeństwa
- Generowanie raportów i analiz
Systemy SMS pozwalają na centralizację informacji związanych z bezpieczeństwem, co ułatwia podejmowanie decyzji oraz monitorowanie trendów w zakresie bezpieczeństwa.
Technologie IoT i czujniki bezpieczeństwa
Internet Rzeczy (IoT) oraz nowoczesne czujniki bezpieczeństwa umożliwiają monitorowanie parametrów bezpieczeństwa w czasie rzeczywistym, co pozwala na szybką identyfikację potencjalnych zagrożeń. Przykładowe zastosowania obejmują:
- Monitorowanie stężenia substancji niebezpiecznych w powietrzu
- Kontrolę parametrów procesowych (temperatura, ciśnienie, przepływ)
- Monitorowanie stanu technicznego maszyn i urządzeń
- Śledzenie lokalizacji pracowników w strefach niebezpiecznych
- Wykrywanie nieprawidłowych zachowań lub warunków pracy
Dane zbierane przez czujniki mogą być analizowane w czasie rzeczywistym, co pozwala na natychmiastową reakcję w przypadku wykrycia potencjalnego zagrożenia.
Wirtualna i rozszerzona rzeczywistość (VR/AR)
Technologie wirtualnej i rozszerzonej rzeczywistości znajdują coraz szersze zastosowanie w procesie oceny ryzyka oraz szkoleniach z zakresu bezpieczeństwa. Kluczowe zastosowania VR/AR obejmują:
- Symulacje sytuacji niebezpiecznych w bezpiecznym środowisku wirtualnym
- Wizualizację potencjalnych zagrożeń i ich konsekwencji
- Interaktywne szkolenia z zakresu procedur bezpieczeństwa
- Wsparcie w przeprowadzaniu inspekcji bezpieczeństwa
- Wizualizację danych dotyczących bezpieczeństwa w kontekście rzeczywistego środowiska pracy
Technologie VR/AR pozwalają na bardziej angażujące i efektywne szkolenia z zakresu bezpieczeństwa, co przekłada się na lepsze zrozumienie zagrożeń i procedur bezpieczeństwa przez pracowników.
Sztuczna inteligencja i uczenie maszynowe
Sztuczna inteligencja (AI) i uczenie maszynowe (ML) znajdują coraz szersze zastosowanie w analizie danych związanych z bezpieczeństwem. Kluczowe zastosowania AI/ML obejmują:
- Predykcję potencjalnych zagrożeń na podstawie historycznych danych
- Identyfikację wzorców i trendów w zdarzeniach wypadkowych
- Optymalizację środków kontrolnych
- Automatyczną analizę obrazu z kamer przemysłowych pod kątem zachowań niebezpiecznych
- Wsparcie w podejmowaniu decyzji dotyczących zarządzania ryzykiem
Technologie AI/ML pozwalają na bardziej proaktywne podejście do zarządzania bezpieczeństwem, koncentrując się na przewidywaniu i zapobieganiu zagrożeniom, a nie tylko reagowaniu na już zaistniałe zdarzenia.

